Amazon’s AI-Powered Warehouse: A Game-Changer in California
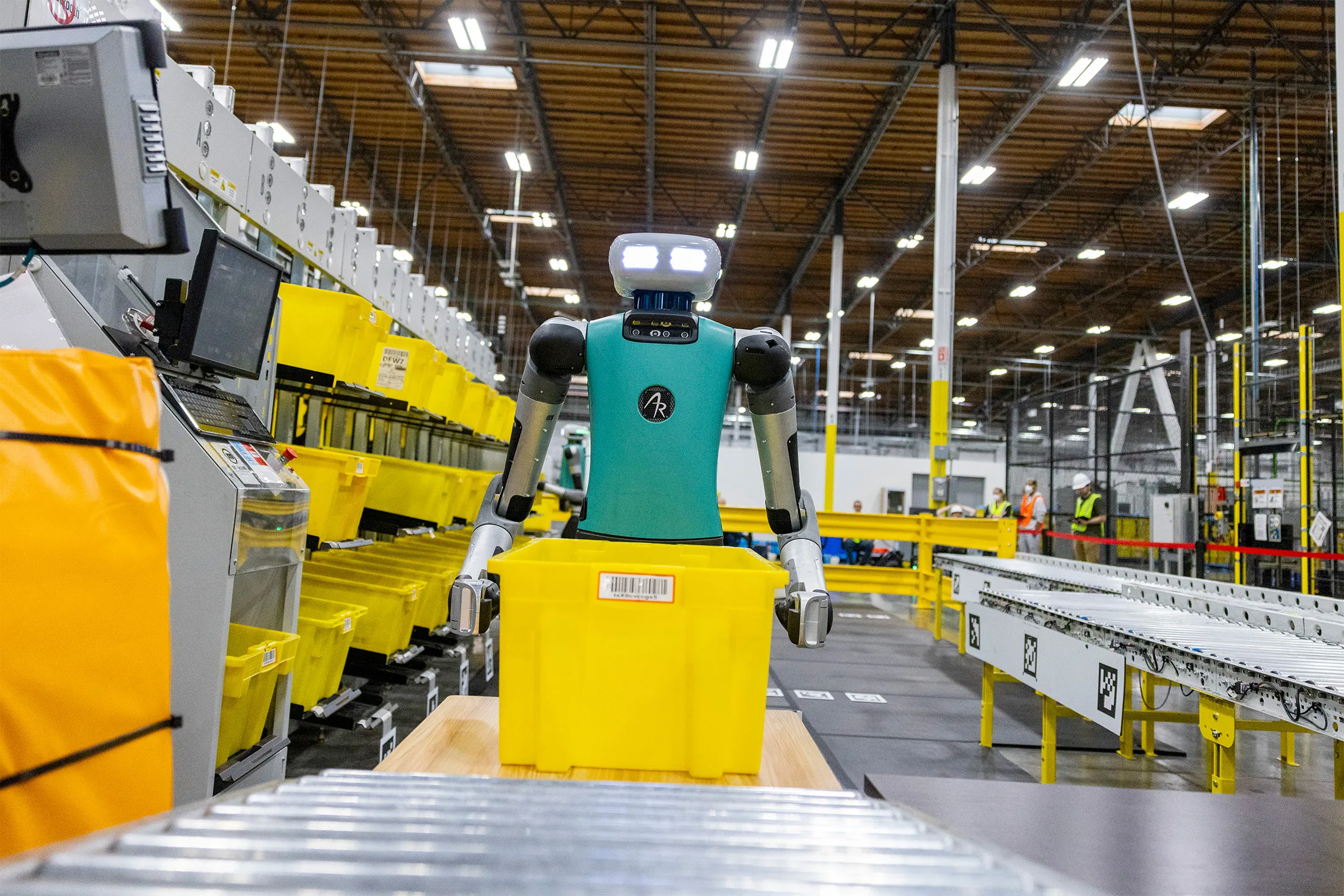
Amazon has rolled out a fully AI-automated warehouse in California, slashing human labor by 60% and doubling the speed of package processing. This isn’t just a small step forward—it’s a giant leap in how the company handles its massive order volume. Here’s the thing: this new warehouse shows what happens when you combine smart tech with real-world logistics. It’s efficient, fast, and a little controversial. Let’s break it down.
How the AI Warehouse Works
Imagine a warehouse where robots zip around, picking, packing, and shipping packages with barely any human help. That’s what Amazon has built in California. The warehouse uses a mix of AI algorithms, robotic arms, and autonomous vehicles to handle everything from sorting inventory to getting boxes ready for delivery. The system, powered by Amazon’s custom “DeepFleet” AI model, figures out the fastest way to move goods, cutting down on bottlenecks and wasted time.
The robots—like Proteus, which navigates around humans, and Sparrow, a robotic arm that grabs individual items—are the stars here. They use computer vision to “see” products and machine learning to get smarter over time. For example, if a popular toy is selling out fast, the AI predicts this and moves more of that toy closer to the packing stations. This setup processes packages twice as fast as older warehouses, handling up to 100,000 orders a day during peak times.
Why It’s So Fast
- Smart Routing: AI picks the shortest paths for robots, avoiding traffic jams in the warehouse.
- Real-Time Decisions: The system adjusts on the fly, like rerouting packages during a sudden demand spike.
- Less Human Error: Robots don’t misplace items or mix up orders, which speeds things up.
The Trade-Offs
Pros | Cons |
---|---|
Faster order processing | High setup costs for tech |
Fewer mistakes in packing | Fewer jobs for workers |
Safer for humans (less heavy lifting) | Workers need new skills |
Impact on Workers: A Double-Edged Sword
Here’s where things get tricky. Cutting human labor by 60% sounds like a win for efficiency, but it’s a tough pill for workers. In this California warehouse, Amazon has reduced its human staff from 1,000 to about 400. The remaining workers mostly oversee the robots, fix tech issues, or handle tasks the machines can’t do yet, like dealing with oddly shaped packages.
I spoke to a friend who used to work in an Amazon warehouse in Ohio. He said the old setup had him walking 12 miles a day, picking items off shelves. It was exhausting, and mistakes were common when everyone was rushing. The new AI system would’ve made his job easier by letting robots do the heavy lifting. But he also admitted, “If this was around back then, I might not have had a job at all.” That’s the reality: automation makes work less grueling for some, but it also means fewer people are needed.
Amazon’s pushing hard to retrain workers through programs like Career Choice, which pays for training in fields like robotics or IT. Since 2019, they’ve spent over $1.2 billion to train 300,000 employees. But not everyone’s thrilled. Some workers feel the new roles are too technical, and retraining doesn’t guarantee a job. Plus, posts on X show mixed feelings—one user, @JesseCohenInv, pointed out that each robot packer can replace 24 workers, sparking debates about job losses.
Why Speed Matters to Amazon
Doubling package processing speed isn’t just about bragging rights—it’s about staying ahead. Customers expect fast delivery, with 66% of shoppers wanting free, next-day shipping, according to a 2025 Sifted report. Amazon’s AI warehouse can process up to 100,000 packages a day, compared to 50,000 in older facilities. That means more same-day deliveries, especially during crazy times like Black Friday.
What this really means is Amazon can keep its promise of speed while cutting costs. Fewer workers and faster robots lower the price per package. This warehouse in California, for instance, uses the Sequoia system, which stores inventory 25% faster than older methods. That efficiency lets Amazon offer lower prices or free shipping, which keeps customers coming back.
What’s Next for Amazon and Workers?
Amazon’s not stopping here. They’ve already got over 750,000 robots across their warehouses, and the California site is a blueprint for more to come. By 2028, they plan to roll out similar setups globally, potentially cutting human labor even further. But there’s a catch: the more they automate, the more they need skilled workers to maintain the tech. That’s why they’re investing in training programs.
For workers, it’s a mixed bag. Some will move into better-paying tech roles, but others might struggle to adapt. The bigger picture? Automation’s reshaping what warehouse jobs look like. Instead of replacing humans entirely, it’s creating a world where people and machines work together—just not in the same numbers as before.